Assiduously innovative companies emerge with new materials as alternatives to leather or polyester, promising to revolutionize the fashion industry. Its purpose is to reduce the environmental footprint and move towards a more circular business.
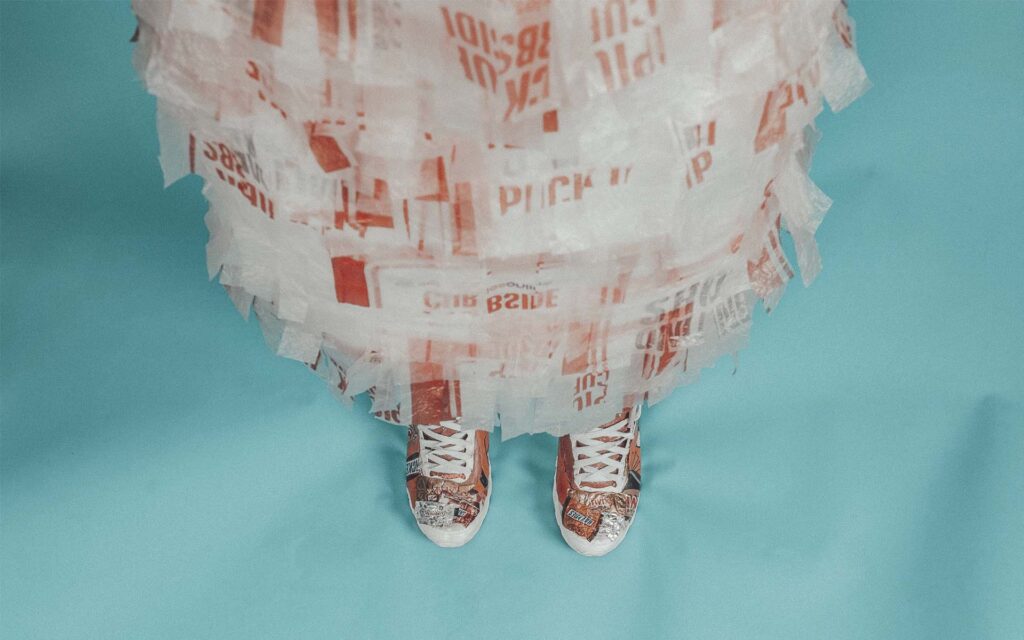
According to the State of the Textile Industry report by the Material Innovation Initiative, investment in “next-generation materials” innovation in 2021 was more than double that of 2020.
It should be noted that the organization considers as new-generation materials as those that directly replace the so-called traditional materials such as leather, silk, and wool. Recycling technologies are excluded from this definition.
However, despite the efforts of these committed companies to develop new alternatives, the process of replacing existing materials with novel ones can be a difficult path to implementation.
Recycling technology
As McKinsey & Co. stated in its report last year, one of the most sustainable and scalable resources is fiber-to-fiber recycling.
It is considered that this type of large-scale recycling can contribute to solving the problem of textile waste. The waste is converted into new fibers and then used in the creation of new garments or other textile products.
According to estimates by the Consultant, 70% of textile waste could be recycled from fiber to fiber. The remaining 30% would require open-loop recycling or other solutions such as syngas production through thermochemical recycling.
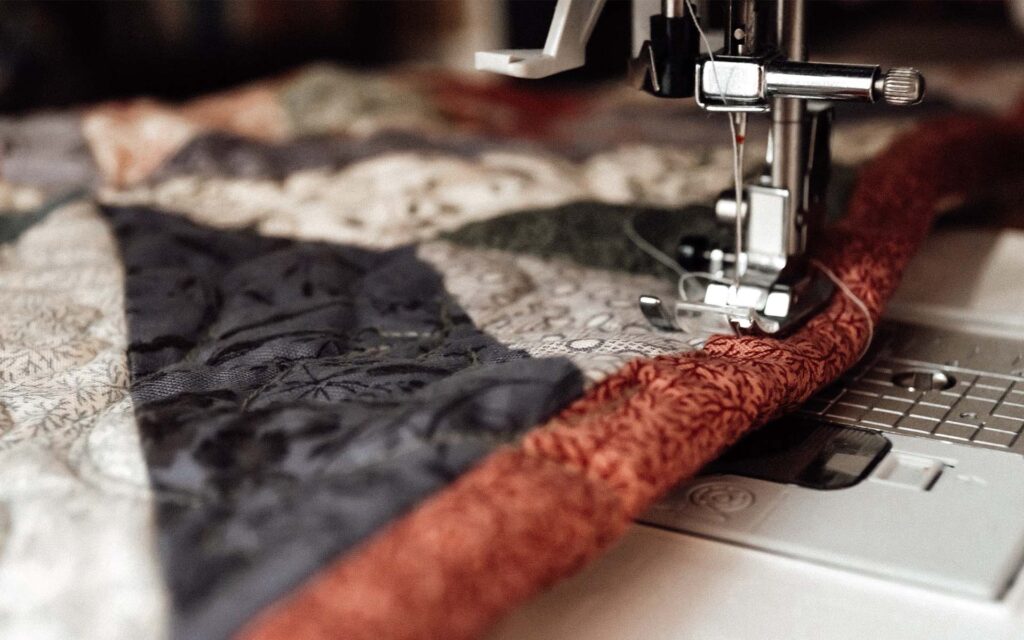
The report “Sorting for Circularity Europe” published last year by the organization Fashion for Good analyzed the nature of the increase in textile waste collected in Europe (due to increased consumption and its disposal) and the infrastructure that needs to be developed to treat it.
Analysis in Belgium, Germany, Spain, the Netherlands, Poland, and the United Kingdom indicates that 74% (representing 494,000 tonnes) of low-value post-consumer textiles are readily available for fiber-to-fiber recycling.
This represents an additional value generation potential of $168 million per year through the reintroduction of sorted and recycled textiles into the value chain.
Limitations
According to the report “Scaling textile recycling in Europe – turning waste into value”, less than 1% of textile waste is recycled from fiber to fiber due to several obstacles that need to be overcome. The strict requirement of fiber composition is one of the most common.
An additional problem is the need for precise classification of textiles based on fiber composition. In addition, elements such as zippers, buttons, and other metallic details are often impossible to remove.
On the other hand, this recycling technology is only used on a small scale.
To reach its full potential, the textile recycling supply chain requires scaling up this technology to an industrial scale. It is necessary to provide enough raw materials, improve production quality, and reduce costs.
“As fiber-to-fiber textile recycling commitments and policies increase, as well as the amount of textile waste collected, the infrastructure needed to drive the shift to circular systems requires significant investment to scale” Katrin Ley, CEO of Fashion for Good
The cost of producing new materials
When it comes to these innovative technologies, one of the biggest impediments is the cost of installations. The production of new materials often requires considerable capital expenditure to build the infrastructure.
Generally, the process begins with a pilot construction, progressing to a demonstration facility before the development of a full-scale structure.
As for the recycling process itself, collection and recycling with complex and expensive procedures is necessary. In addition, the chemicals used are often also expensive.
In the 2019 McKinsey & Co. survey, procurement executives believed it is necessary to invest in building manufacturing capacity to increase material availability. And since investments are considered the biggest obstacle to implementation, only 26% of companies are willing to invest.
The Case for New Bolt Threads Materials
In the middle of this year, Bolt Threads announced a pause in the production of Mylo, its alternative to leather created from mycelium (fungus). Its decision has been necessary due to the difficulties in obtaining new investments and the increase in costs. This has highlighted the obstacles faced by alternative materials.
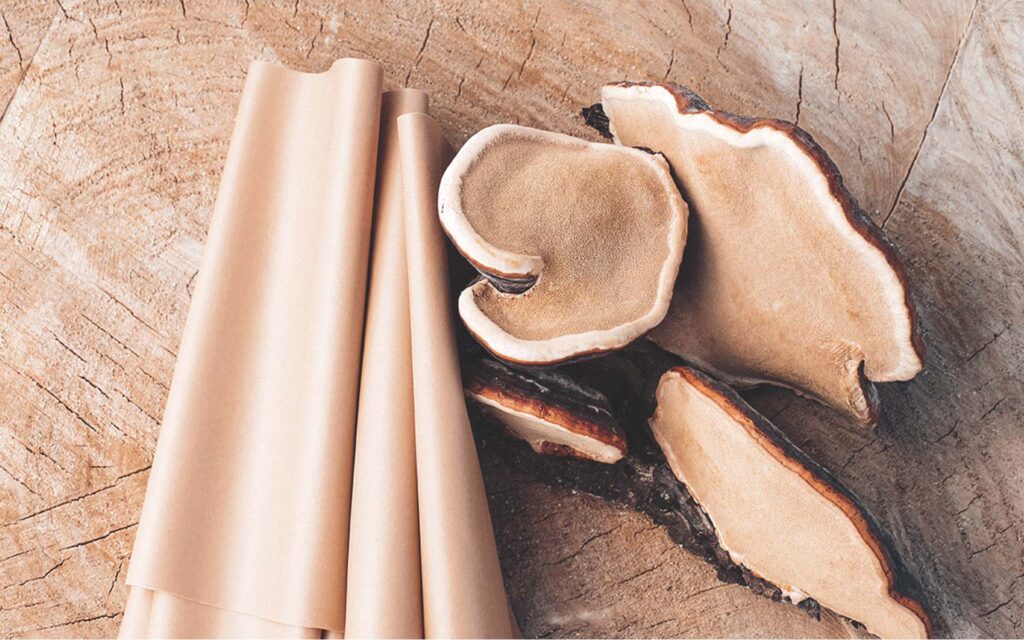
“Despite our intensive efforts, the current macroeconomic climate has made it increasingly difficult to secure the capital needed to support the scaling up of emerging technologies,” the company said in its statement.
Since its founding in 2009 in California, the company has collaborated with designer Stella McCartney, Danish fashion firm Ganni, and sportswear firm Lululemon. The Kering Group and Adidas committed to developing products with Mylo.
To manufacture this material, Bolt Threads has designed a process to grow mycelium in a vertical cultivation facility powered by 100% renewable energy. It has transformed it into a material with the appearance and feel of animal skin being less harmful to the environment.
During this time, the company raised more than $300 million in various funding rounds.
Dan Widmaier, the company’s founder, and CEO, told Vogue Business that Mylo was close to its commercial scale, but was derailed by inflation and fewer funding opportunities in a weak economic backdrop.
He added that investors’ attention has shifted to new areas, such as artificial intelligence.
The case of Renewcell
Renewcell is a textile recycling company based in Sweden, whose rapid growth is due to its unique technology and its Circulose® product.
Circulose® is a solvent pulp that is manufactured from 100% textile waste with high cellulose content, such as worn cotton jeans.
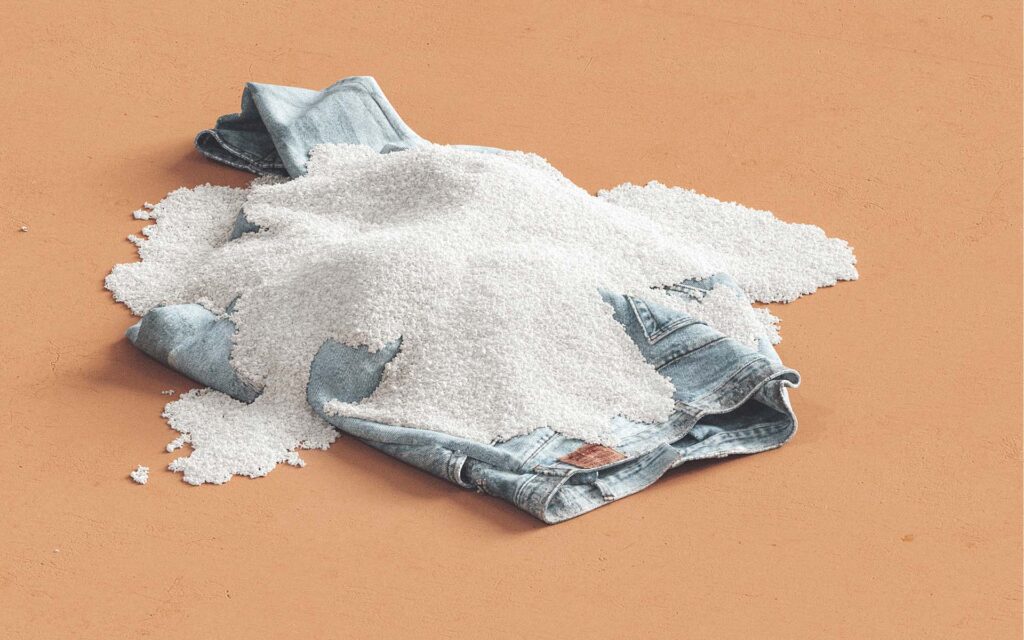
These fibers are spun, woven, or knitted, and then cut and sewn into new, high-quality textile products.
Solvent pulp cellulose is used to make viscose, lyocell, modal, acetate, and other types of regenerated fibers.
The big difference with Circulose® is that it is made from textile waste rather than new cotton, petroleum, or wood.
While the company plans to recycle the equivalent of more than 1400 million T-shirts a year by 2030, its technology has limitations. You can only recycle cotton garments, with a tolerance of up to 5% of content other than this fiber.
“Partly because it is difficult to separate polyester, the excess of which affects product quality, but also because we want to make sure we get a decent performance,” explains Harald Cavalli-Björkma Chief Strategy Officer.
Innovative technologies and new materials are critical to reducing the negative impact of the fashion industry. That is why organizations and companies must rethink their importance.
According to McKinsey & Co and the Global Fashion Agenda, following the current path, the industry will not be able to reduce the greenhouse gas emissions needed under the Paris Agreement or meet the UN Sustainable Development Goals in time for 2030.