Nowadays, many fashion companies are moving their production to their home country. They want to reduce costs while contributing to sustainability.
It is a widely recognized fact that the fashion industry is considered one of the most polluting industries in the world due to its great negative impact on the environment.
In recent years, this sector has undergone a drastic transformation with the emergence of fast and ultra-fast fashion, which is one of the biggest problems facing the planet today and will affect future generations.
Offshoring
Historically, numerous fashion companies have benefited from the offshoring process.
Offshoring is a business practice that consists of moving production to countries where labor and tax conditions allow for lower manufacturing costs, resulting in higher profits.
Although the final stage of production is carried out in one country, it is likely that the raw materials may even come from another continent; being different from the place of marketing and consumption.
Companies that opt for this strategy and, for example, move their production to Asia or developing countries, although they are guaranteed lower costs, they lose control of the working conditions of the people who make the garments.
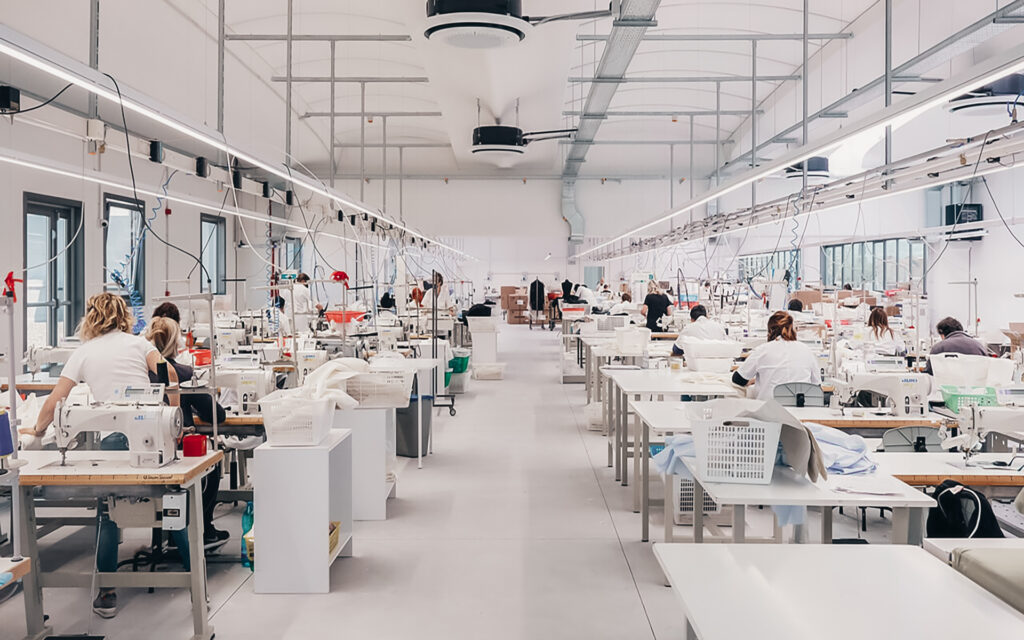
Developing countries are important markets for garment manufacturing. They are poor countries with weak labor regulations that make it easier for firms to pay lower wages to workers who generally work in unsafe conditions.
This trade strategy is believed to have arisen with the elimination of the Multifiber Arrangement, which regulated global trade in textile and clothing products between two countries.
With the elimination of quotas imposed on international textile trade, many firms moved their production chain to Asia to reduce their costs.
But it is not only fast fashion firms that are sourcing from supply chains in other countries. The luxury sector also has foreign suppliers.
With international manufacturing, firms must consider not only manufacturing lead time but also delivery time.
The COVID-19 pandemic exposed the major problem of production outside the home country. As borders closed, companies that relied on foreign-made raw materials and garments were unable to obtain them, leaving many global suppliers without payment.
Bureaucratic bottlenecks and increased shipping costs were reasons for companies to start considering returning to their homelands.
“Demand volatility is one of the main reasons procurement managers gave for adapting their supply chains, as post-shutdown recovery and spikes in demand strain production and transportation capabilities,” said Matt Powell, an analyst, and consultant with market research firm NPD to Vogue Business.
Back to the roots
While offshoring leads to higher profits, the textile industry is beginning to rethink its production chain.
According to a McKinsey & Company report, which asks whether garments are coming home, consumers are increasingly aware of the environmental impact of linear clothing production models.
It also states that around 78% of people said that sustainability is very likely to be a key purchasing factor for consumers between now and 2025.
According to the report, one of the biggest challenges today is the sourcing of raw materials and fabrics. Only a located value chain offers the speed and flexibility of the supply chain.
Reshoring
It is the relocation of production.
It is the process of returning the manufacturing of domestic products from a foreign country to the home country.
Reshoring involves investing in one’s own country, boosting the local labor market, improving economic growth, and developing relationships with local suppliers.
Nearshoring
It is another alternative to relocation. It involves moving production closer for better logistics and more control, and transferring work to another company that is located within its own region.
Benefits
- Reduces greenhouse gas emissions
- Reduces the risk of increased pollution
- Ensures shorter purchasing times
- Optimizes logistics costs
- Generates greater control of operations
- Reduces regulatory issues
- Increases transparency in the production chain
- Attracts engaged consumers
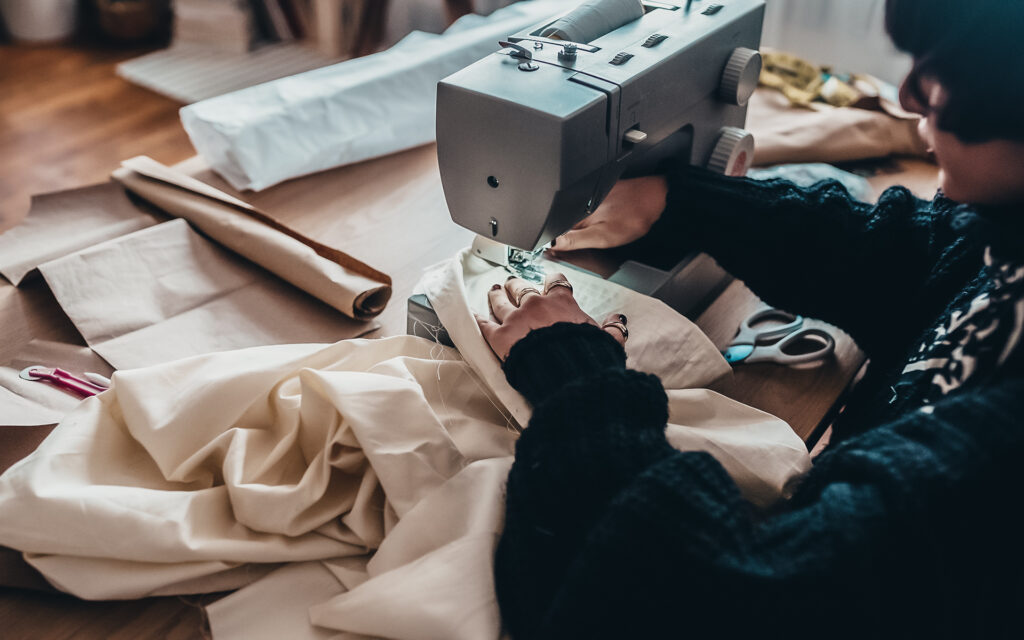
Firms in action
Italian firm Benetton is one of the companies that is moving production closer to its home country, such as Turkey, Serbia, and Egypt. Its aim is reducing low-cost manufacturing production in Asia.
According to its CEO Massimo Renon “It is a strategic decision to have more control over the production process and also over transportation costs”.
The Hugo Boss firm is another example of a company that is committed to producing close to where it markets its products.
“Near-shoring has gained popularity in recent months due to recent capacity shortages, bottlenecks in the global logistics infrastructure, and increased global demand,” says the firm’s head of global corporate communications.
Recently, PVH Corp. (the U.S. company that owns Tommy Hilfiger, Calvin Klein, and also holds the Michael Kors license) closed one of its factories in Ethiopia due to allegations of human rights violations in the country.
This shows that international manufacturing is not always the best option.
El caso Manteco
Manteco is an Italian company created in the 1940s that specializes in high-quality textiles.
With its own denomination of origin, it pays special attention to the circularity and sustainability of its wool through innovative solutions.
It has a high range of colors of regenerated wool (MWool®) through the Recype® process.
This Italian house has worked with luxury brands such as Dior and Prada, and has even collaborated with the fast fashion brand Zara.
Since its inception, sustainability has been a major part of its DNA.
That is why it has MantEco for Planet®, a roadmap aligned with the 17 sustainable development goals of the UN Agenda 2030, which has been awarded the “Radical Green” award.
In addition, they are members of the Ellen MacArthur Foundation Network.
Manteco is constantly pursuing growth and expansion objectives, with an eye always directed toward enhancing the values of sustainability.
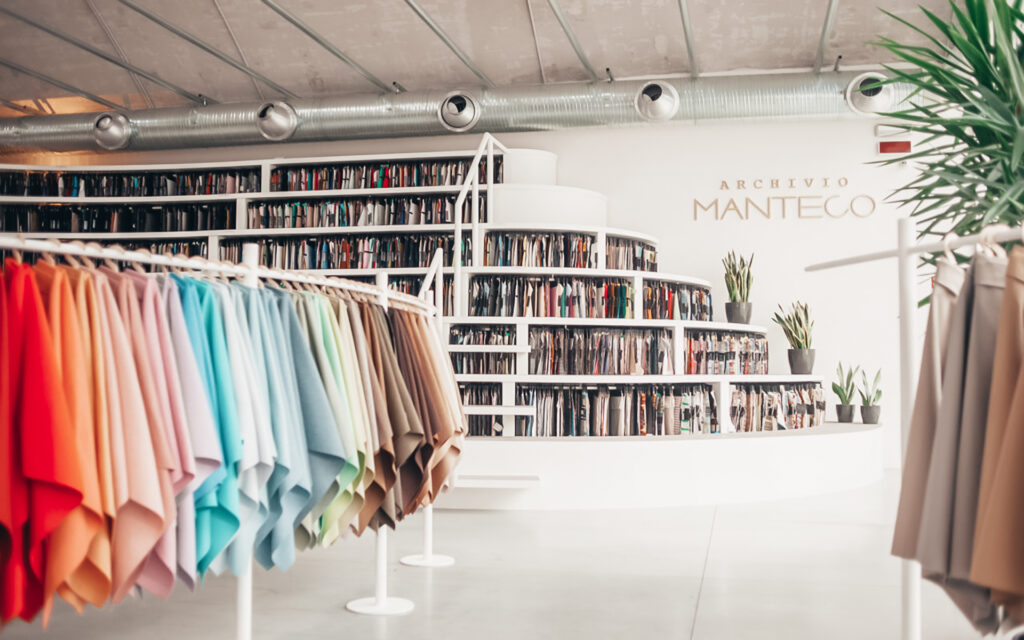
By returning manufacturing to its country of origin, firms not only have greater direct control over the entire production chain, but are also making a major contribution to sustainability.